Ekofisk tank – an icon set to stay
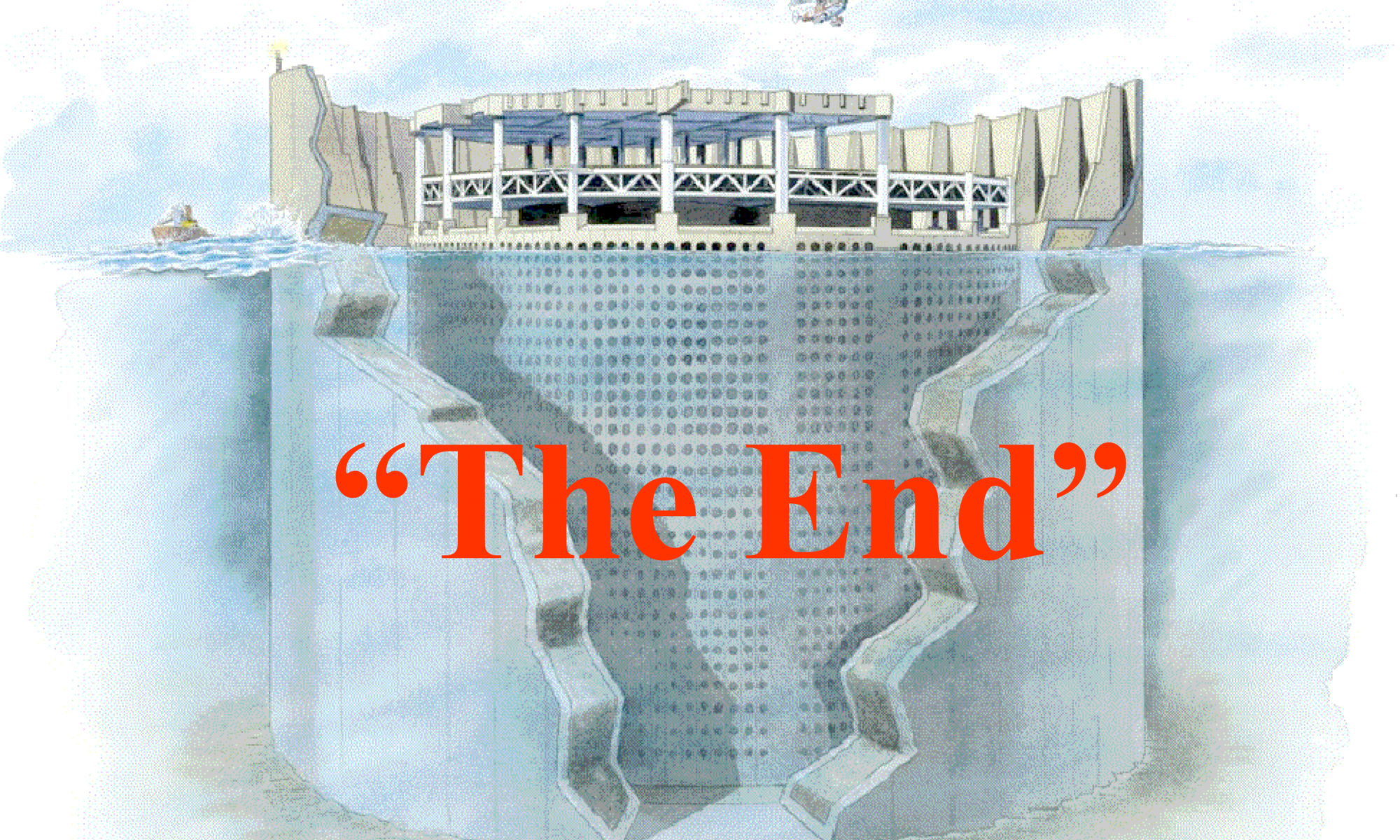
The wide-ranging job of preparing the Ekofisk I cessation project began in 1994, with the plans submitted to the government in October 1999 and various revisions in April 2001. Particular attention was paid in this context to that concrete giant, the Ekofisk tank, and its associated breakwater, and separate proposals for its future were delivered in January 2002.[REMOVE]Fotnote: Proposition no 51 (2001-2002) to the Storting, Om disponering av Ekofisk-tanken med beskyttelsesvegg.
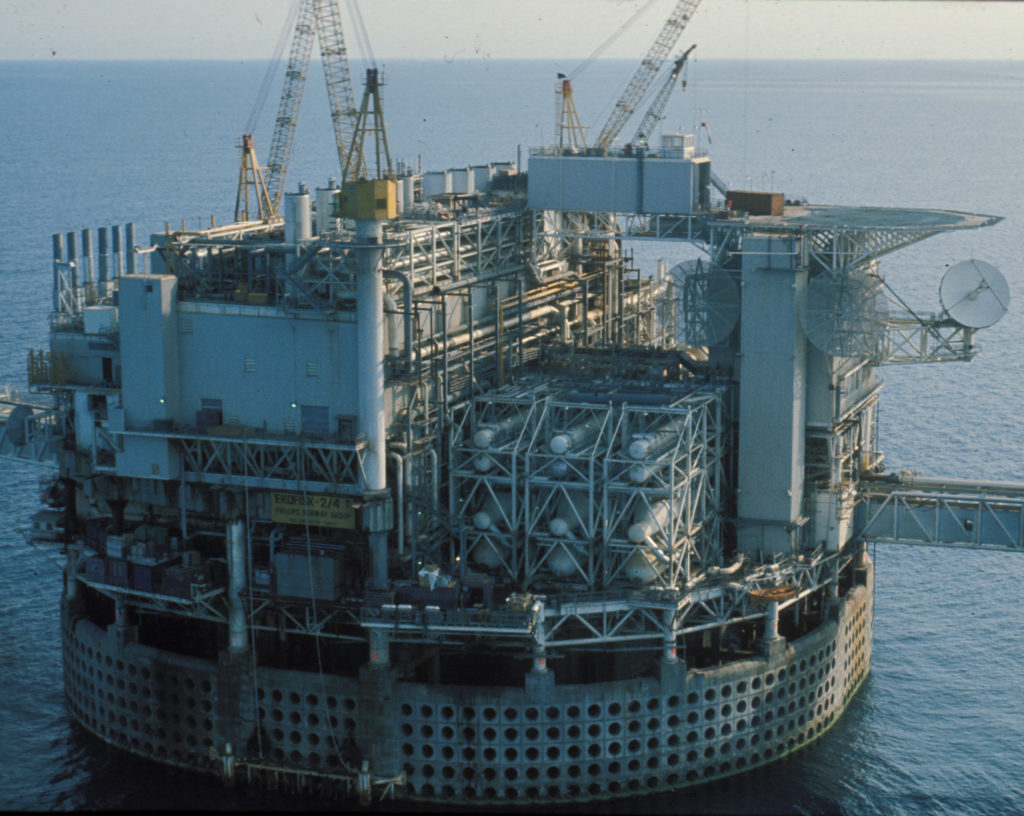
Ekofisk 2/4 T had been installed on the field in 1973. It was originally intended to store crude, but that role disappeared when the oil pipeline to Teesside in the UK opened. The tank has subsequently had various applications, including as the base for process facilities and a treatment plant for produced water.
A breakwater was installed in 1989 to protect the structure against increased wave forces after its freeboard had been reduced by seabed subsidence on Ekofisk. Various disposal options were identified through a brainstorming process. An extensive programme of technical and scientific studies reduced them to three:
- tank and breakwater remain standing on the field, but the superstructure is removed and the interior cleaned
- the superstructure is removed, and tank and breakwater are towed to a suitable site for scuttling in deep water
- tank and breakwater are brought to land for recycling.
In order to identify the most relevant of these ideas and come up with a recommended solution, the Ekofisk licensees assessed each proposal in relation to a set of criteria. These were the technical feasibility of the plans, the safety risk involved, their environmental impact, the economics and the impact on society. It quickly became clear that the technical challenges and financial cost of removing such an installation meant these options would face substantial opposition. On the other hand, many people questioned whether safety against oil spills could be guaranteed. The environmental organisations were particularly sceptical. Operator Phillips accordingly carried out a detailed study of the options in a separate impact assessment which took several years to complete. The conclusion was very clear – leaving behind the concrete tank, its integrated superstructure and the breakwater represented the best option.[REMOVE]Fotnote: Phillips Petroleum, Epoke – Informasjon om sluttdisponering av Ekofisk I, no 10, April 2001.
On behalf of the Phillips group of licensees as well as A/S Norske Shell and Norpipe Oil AS, Phillips submitted a report on 22 October 1999 to the Ministry of Petroleum and Energy.[REMOVE]Fotnote: Phillips Petroleum, Avvikling og disponering av Ekofisk I, Konsekvensutredning, 1999.
The latter presented its recommendations in a separate proposition (Bill) to the Storting (parliament), which approved leaving the tank and breakwater in situ. Two integrated decks, one above the other, needed be retained in order to stabilise the structure and ensure helicopter access for future inspections. The tank had to be marked on navigational charts, and signal equipment to safeguard shipping and helicopter traffic to the Ekofisk field had to be installed.[REMOVE]Fotnote: Proposition no 51 (2001-2002) to the Storting, Om disponering av Ekofisk-tanken med beskyttelsesvegg.
A separate study to see whether it would be feasible to refloat the tank had been conducted by RaKon, a specialist in inspection, monitoring and rehabilitation of concrete structures.[REMOVE]Fotnote: RaKon website, accessed 29 March 2019.
This quickly established that the best option was to tie tank and breakwater together and then tow them to land as a unit. Removing the breakwater first meant the tank would have to stand unprotected for a whole winter season. The structure would very probably suffer damage from tough North Sea storms in this period. It was therefore agreed to look at a “combined” solution using a special “floor” structure to ensure buoyancy during a tow. A dedicated team of technical experts risk-assessed the operation. Their results were also checked by Det Norske Veritas (DNV), Norway’s most reputable specialist in this field. These evaluations showed that all the options had a probability of failure with serious consequences which exceeded the acceptable limits set for such possibilities.
DNV also carried out an impact assessment of the three options in terms of their environmental effect, which took seven factors into account. Two in particular were found to have negative consequences for option 1 compared with removal from the field – lack of resource utilisation of the steel and concrete materials, and the pollution aspect of leaving behind something alien to the site. However, letting the tank stay on the field was considered advantageous in terms of energy consumption (almost a halving) and emissions to air compared with the removal options. Together with project execution specialist Asplan Viak in Stavanger, DNV moreover assessed the social consequences of the three main options.
Leaving the structures in place would have little or no influence on fishing or shipping in the area. The cost was also minimal compared with either of the removal proposals.
NOK 2.5-3.5 billion would be needed for both of the latter. Moreover, scuttling in a fjord would be unacceptable to various organisations in several countries around the North Sea basin.[REMOVE]Fotnote: Phillips Petroleum, Epoke – Informasjon om sluttdisponering av Ekofisk I, no 10, April 2001.

Before a discussion could even begin on removal or not, Phillips had to clarify the actual contents of the storage tank – a job which took three years from 1998 to 2000. Cores and water samples were taken from several of the cells and annular spaces, and sent continuously to land for analysis. The key question was how clean is clean enough. Phillips based its answer on guidelines issued by the Norwegian Pollution Control Authority (SFT), which categorised levels of pollution in five classes.
Class | Description | Colour code |
1 | Insignificant – little pollution | Blue |
2 | Moderate pollution | Green |
3 | Marked pollution | Yellow |
4 | Heavily polluted | Orange |
5 | Very heavily polluted | Red |
This guidance and classification were amended in 2007. In consultation with the SFT, Phillips chose to set the limit for an acceptable level of pollutants in the bottom sediments at class 2. Should pollution exceed this limit in certain areas, a special assessment was to be made of whether measures had to be taken and what these should be. Results from the sampling showed that the concentration of PAH[REMOVE]Fotnote: Polycyclical aromatic hydrocarbons (PAH) are organic compounds of carbon and hydrogen built up from two or more five- and six-membered rings. and several heavy metals – particularly mercury and zinc – was as high as class 5 in some areas. According to the analyses, too, volumes of PCBs[REMOVE]Fotnote: Polychlorinated biphenyls (PCB) are a group of chemical compounds derived from biphenyls, where two or more of the hydrogen atoms in the molecule are replaced by chlorine atoms. which corresponded to class 4 were to be found in the inner and outer annular spaces.[REMOVE]Fotnote: Phillips Petroleum, Epoke – Informasjon om sluttdisponering av Ekofisk I, no 10, April 2001.
The conclusion was that the Ekofisk tank had to be cleaned before it could be allowed to remain on the field, and Phillips launched a study to answer the following questions:
- how was hydrogen sulphide to be handled?
- what was the best way to access the cells?
- what should be done with oil/wax deposits in the cells?
- would anything need to be done with the internal walls in the cells?
- how should bottom sediments in the cells and annular spaces be treated?
- how should the water be treated?
The work was done as an internal exercise in three stages, which also drew on information from many different external companies. More than 50 different options were presented in all. These methods were then assessed in relation to criteria which covered personnel safety, environmental impact, costs, technical feasibility and assessments of public opinion. After several rounds of consideration, an overall solution was proposed which rested on several possible approaches. These in turn were subject to a detailed technical assessment. The final step was to rank measures in relation to the specified criteria, which yielded a total solution involving a specific method for each of the main factors in the clean-up.
In the proposed solution, the questions were tackled one by one. Hydrogen sulphide was to be pumped out through manholes in the top of each storage cell, for instance. Part of the topside equipment had to be removed to access these entry points, while the water in the cells had to be treated to reduce its content of hydrogen sulphide. This treatment consisted of adding a nitrate blend – a process which was time consuming and also had to be kept under careful control.
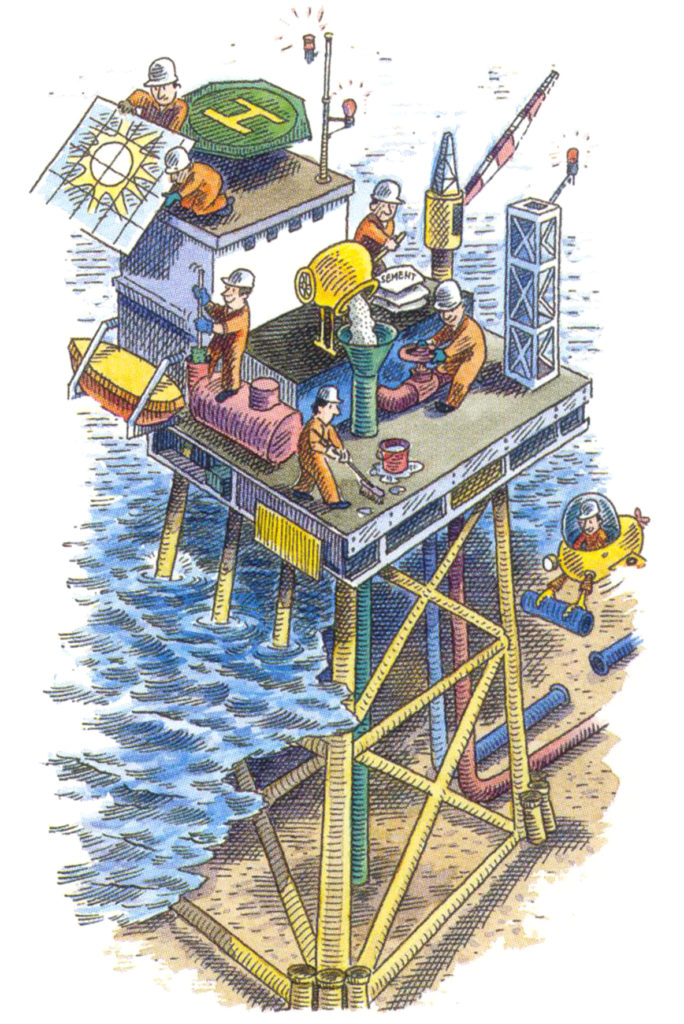
Once the hydrogen sulphide had been reduced to an acceptable level, work could begin to remove the oil/wax deposit at the top of each cell. The narrowness of the access called for the development of special equipment to handle this job. It had to both clean the ceiling and remove the coating by skimming the water. Because the tank cells had been filled with only water since the mid-1970s, oil deposited during storage was assumed to have been washed out and replaced with a new biological film. No technical or chemical solutions were recommended, because this film would probably decay over time without damaging side-effects.
Sediments in the cells and the annular spaces were removed with the aid of remotely-operated sludge suction. While remotely-operated vehicles (ROVs) could operate in the annular spaces, special equipment developed for shutting down and disassembling nuclear power stations was used in the cells. Water and sludge were sucked up to the deck, where a treatment plant had been installed. This comprised cyclones, separators and filter units. After removing sludge and hydrocarbons, the water could be recirculated or discharged overboard – providing it was sufficiently clean. The separated sludge and hydrocarbons were collected in a dedicated tank before being transferred to the Ekofisk 2/4 X platform for injection back into the sub-surface.
Proposition no 51 (2001-2002) was considered by the Storting on 11 June 2002, and the government’s recommendation was unanimously accepted without debate. ConocoPhillips (as the operator had now become) could thereby start awarding the necessary contracts for preparing the tank and taking away its superstructure.
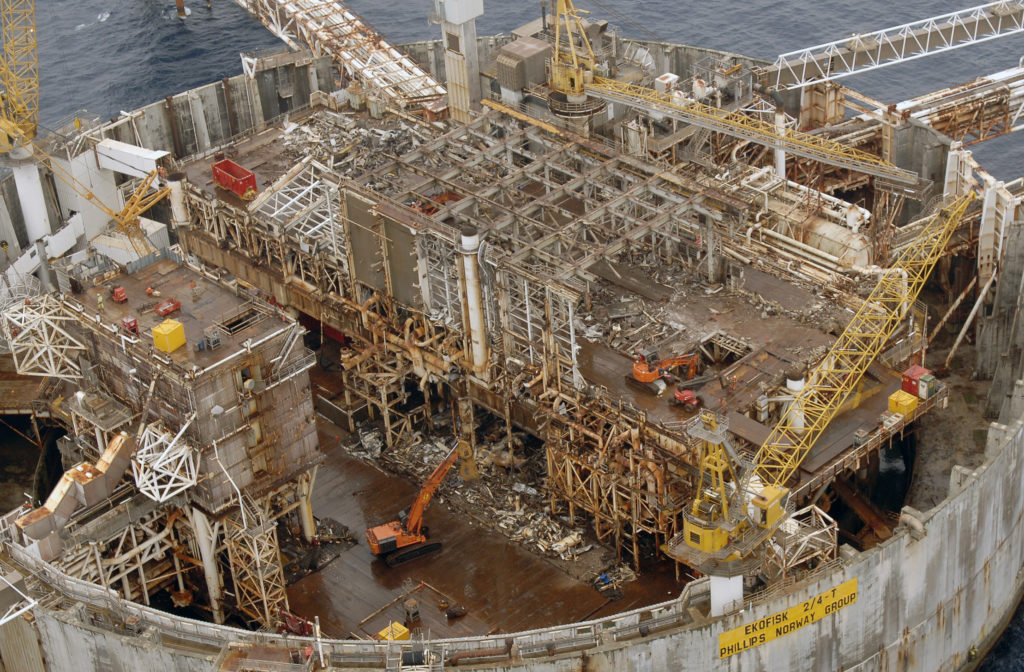
Removing the latter, which weighed just over 24 000 tonnes, was assigned to AF Decom. The offshore work started once the clean-up has been finished.
The tank superstructure was demolished with the aid of excavators fitted with cutters – an approach used for a number of such jobs on land, including the Sola refinery in Tananger. Structures were cut into pieces and roughly sorted offshore before being placed in containers. These were carried by supply ships to Raunes for final sorting. Finally, the scrap was shipped to a recycling facility or for possible deposition. The goal of achieving a recycling factor of 97-98 per cent was met.[REMOVE]Fotnote: ConocoPhillips, “Anlegg for landdisponering blir klargjort”, Nordsjø-Pioner, December 2004.
The demolition job finished on 11 May 2007, when the final consignment of scrap from the steel superstructure was shipped to AF Decom’s facility at Vats north of Stavanger.[REMOVE]Fotnote: ConocoPhillips, “Pionér også i sistevers”, Nordsjø-Pioner, no 3, April 2007.[REMOVE]Fotnote: ConocoPhillips, “Slutt på Ekofisk-tanken”, Nordsjø-Pioner, no 5, June 2007.
Cleaning the tank was carried out in two phases, starting with the storage cells and followed by the extensive job of removing the superstructure. Cell cleaning began in the summer of 2004 and was completed in the course of a year. Structural demolition then started in the summer of 2005 and took almost two years.
The second cleaning phase, covering the annular spaces, got under way in the second quarter of 2007, and was finished in late 2008. It was not until the summer of 2009 that the Ekofisk tank was finally declared to be in resting condition – after serving ConocoPhillips and Norway for more than 30 years since 1973.