Developing the field
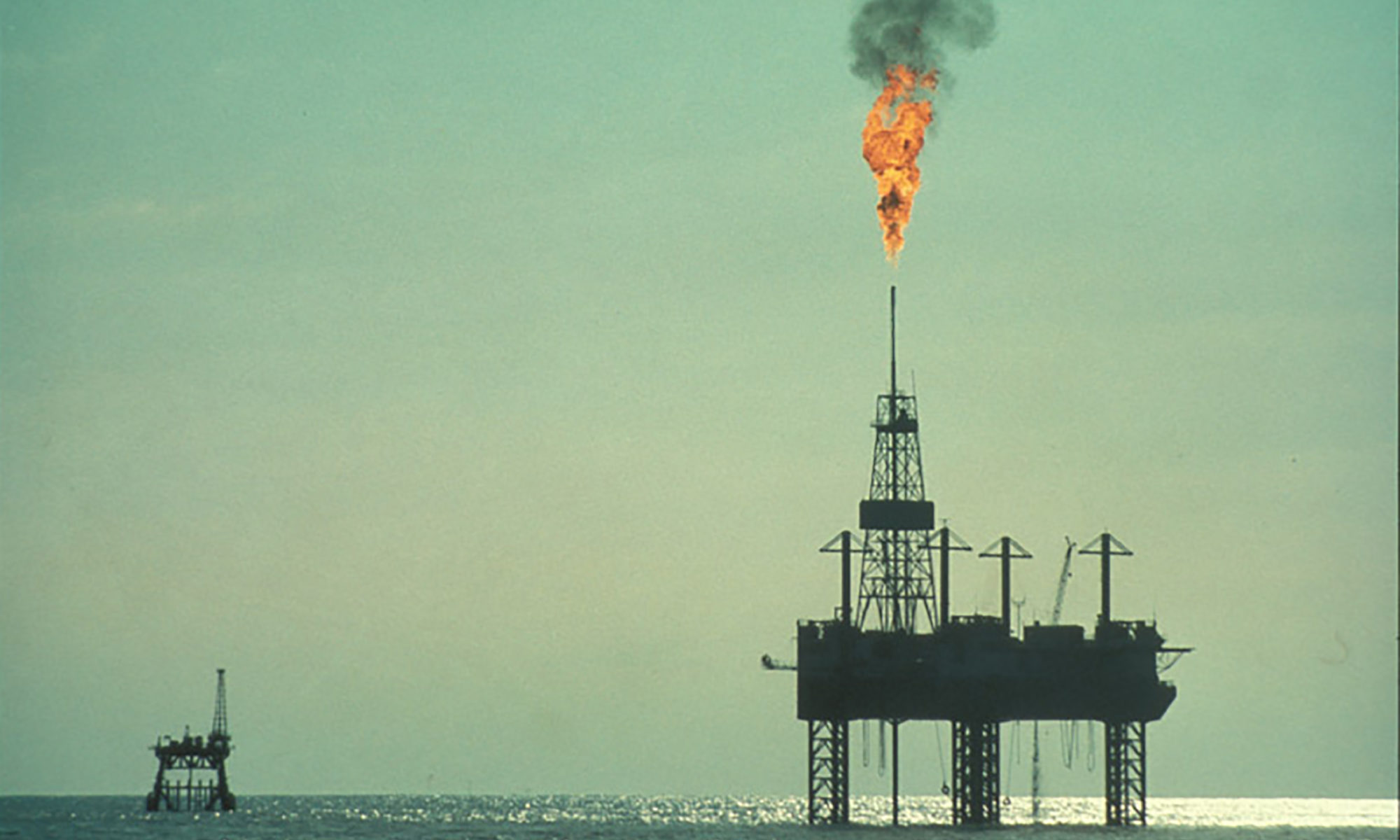
Gulftide was converted to cope with conditions on Ekofisk in the Åmøy Fjord near Stavanger. This jack-up drilling rig was equipped with process equipment and its derrick, helideck, hangar and legs were reinforced.
To win time, it was decided that the discovery well and three appraisals drilled on Ekofisk by Ocean Viking would be completed for production.
Principles for producing from Gulftide were relatively simple. Output flowed from the subsea wellheads to the platform, where it went through two-stage separation to remove gas and water.
With pressure also reduced, the gas was flared off and the oil sent on by flowlines to two loading buoys where shuttle tankers moored to take on cargo.
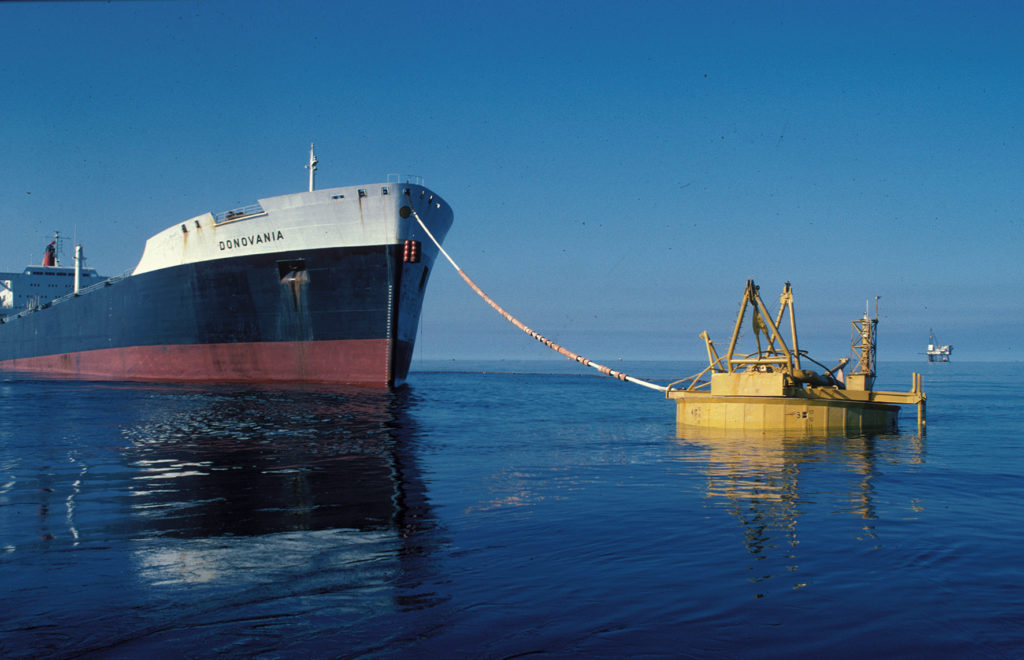
Production could only continue while ships were loading. As soon as one tanker had been filled, the oil stream was diverted to the vessel waiting at the other loading buoy.
The problem with this approach was manifested when weather conditions – strong winds and/or high waves – forced the tankers to leave the buoys.
If that happened, production from the wellheads had to be suspended immediately. Given the prevailing weather on Ekofisk, that happened regularly. Output was halted for 20 per cent of the time during the first year.
Fixed platforms
Gulftide was replaced as the temporary production installation in 1974 by the permanent Ekofisk 2/4 A (Alpha) and 2/4 B (Bravo) platforms for production, drilling and quarters.
In addition came the Ekofisk 2/4 C (Charlie) production, drilling and compression facility, the Ekofisk 2/4 FTP (field terminal platform) for production and risers, and Ekofisk 2/4 Q for accommodation.
Oil and gas were produced by 2/4 A, B and C through their own wells for processing in their separation plants and piping on the 2/4 FTP for a three-stage separation process.
At the same time, the tanker loading buoys were moved further from the platforms and the Ekofisk 2/4 T oil storage tank became operational.
This facility was extremely advantageous, because it allowed production to continue virtually regardless of whether bad weather prevented tankers from connecting to the buoys.
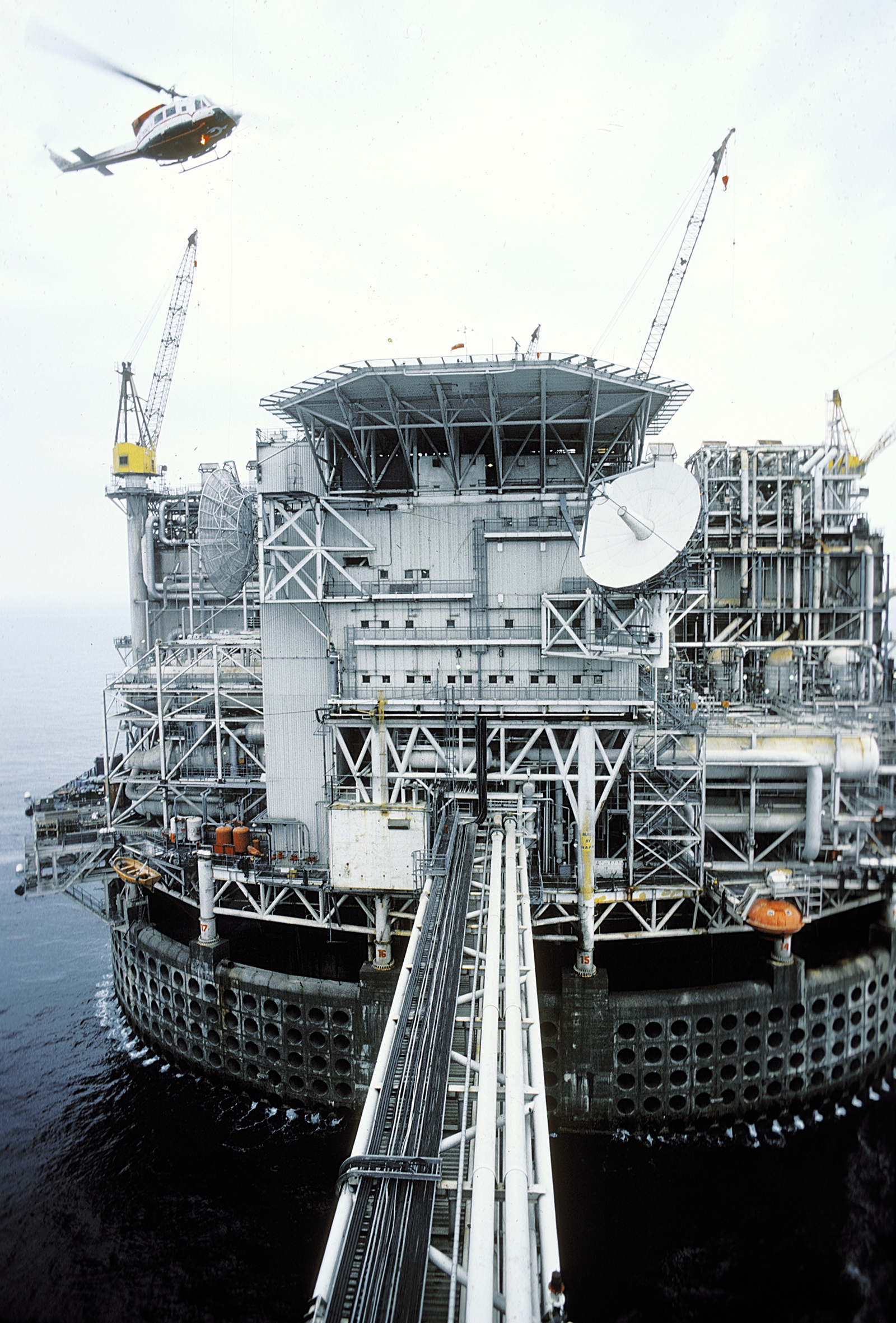
The 2/4 FTP platform, where oil and gas from the three producing facilities was processed, had been planned to handle the level of output estimated for the main field.
Clear restrictions had been imposed by the Norwegian government on the amount of gas Phillips was allowed to flare. That also set a ceiling for oil production, since gas accompanies it up from the reservoir.
The solution was to install two powerful compression packages on 2/4 C in order to inject the gas under pressure back into the producing formation.
Accommodation facilities had to be provided on the two first platforms, 2/4 A and B. Where 2/4 C and FTP were concerned, however, they were tied together with bridges and to 2/4 Q.
When some one searches for his necessary thing, therefore he/she wants to be available that in detail, thus
that thing is maintained over here.
Great article! We will be linking to this particularly great post on our
website. Keep up the great writing.
I am actually grateful to the owner of this
site who has shared this enormous paragraph at at this place.
Howdy just wanted to give you a quick heads up. The words in your post seem to be running off the screen in Ie.
I’m not sure if this is a format issue or something to do with web browser
compatibility but I thought I’d post to let you know. The style
and design look great though! Hope you get the issue resolved soon. Kudos
Howdy! I just wish to give you a big thumbs up for your excellent info you have here
on this post. I will be coming back to your blog for more soon.
I’m really impressed along with your writing talents and also with the layout on your weblog.
Is that this a paid subject matter or did you modify it your self?
Anyway keep up the nice high quality writing,
it’s uncommon to see a great blog like this one these days..
Google Analytics Alternative