Jacking provides the solution
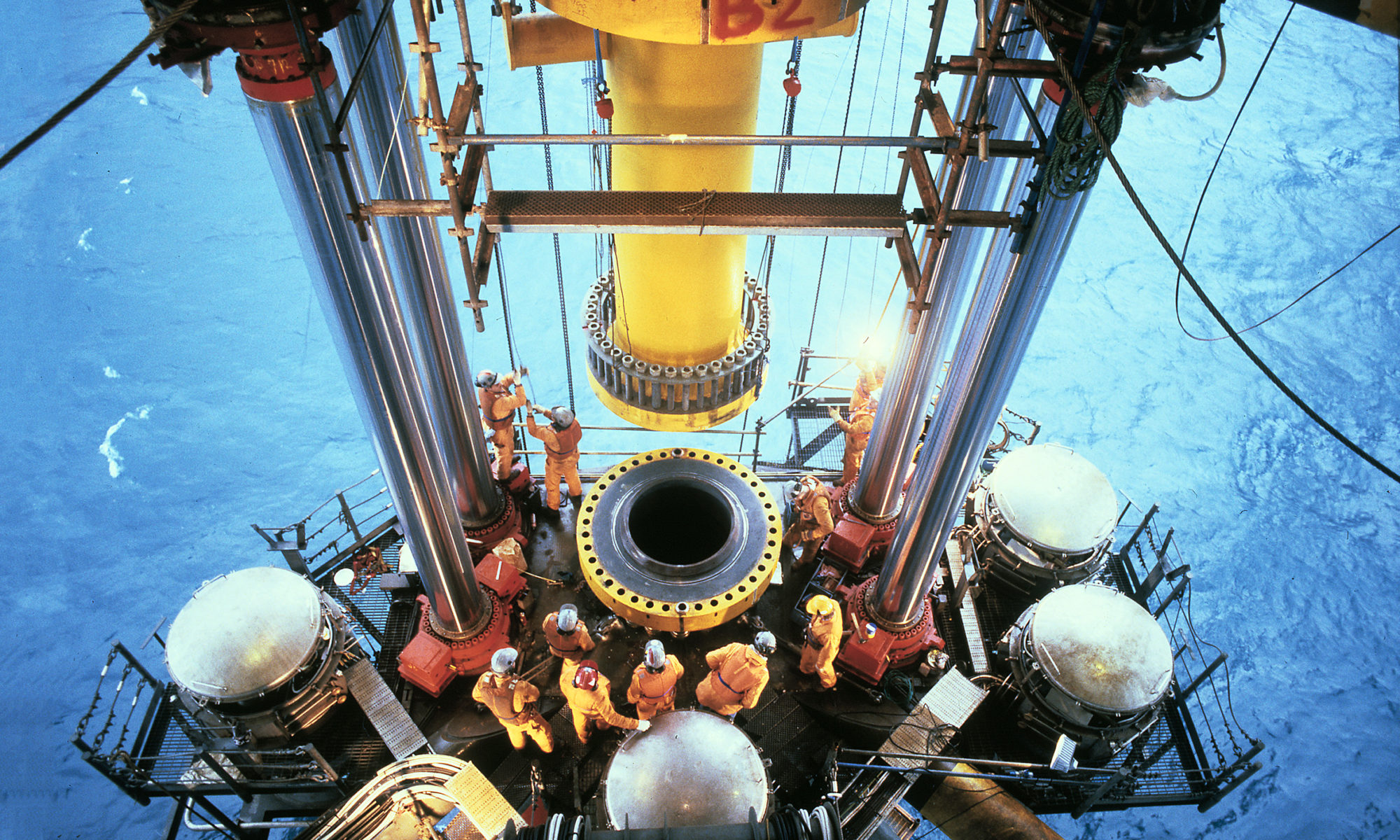
That was primarily done to improve recovery. After it became clear that the seabed over the field was subsiding, however, the amount of gas returned was increased in a bid to counteract this.
But it was not enough. At least 30 different methods for overcoming the problem were discussed, involving engineers from all over Europe.
Jacking up the platforms to restore the air gap between their topsides and the sea surface was an early proposal. This was quickly rejected as unrealistic given the size of the structures and the number of tubulars and pipelines involved.
Once all the other options had been assessed, however, jacking remained as the only viable candidate and the final decision to undertake this process was taken in 1986.
Eight steel platforms, two flare stacks and the bridge supports were involved. Like so much else on Ekofisk, the project involved breaching barriers, finding new solutions and applying them.
Over an 18-month period, about 120 jacks were manufactured while hydraulic actuators and other control systems were readied. Everything was ready by the summer of 1987.
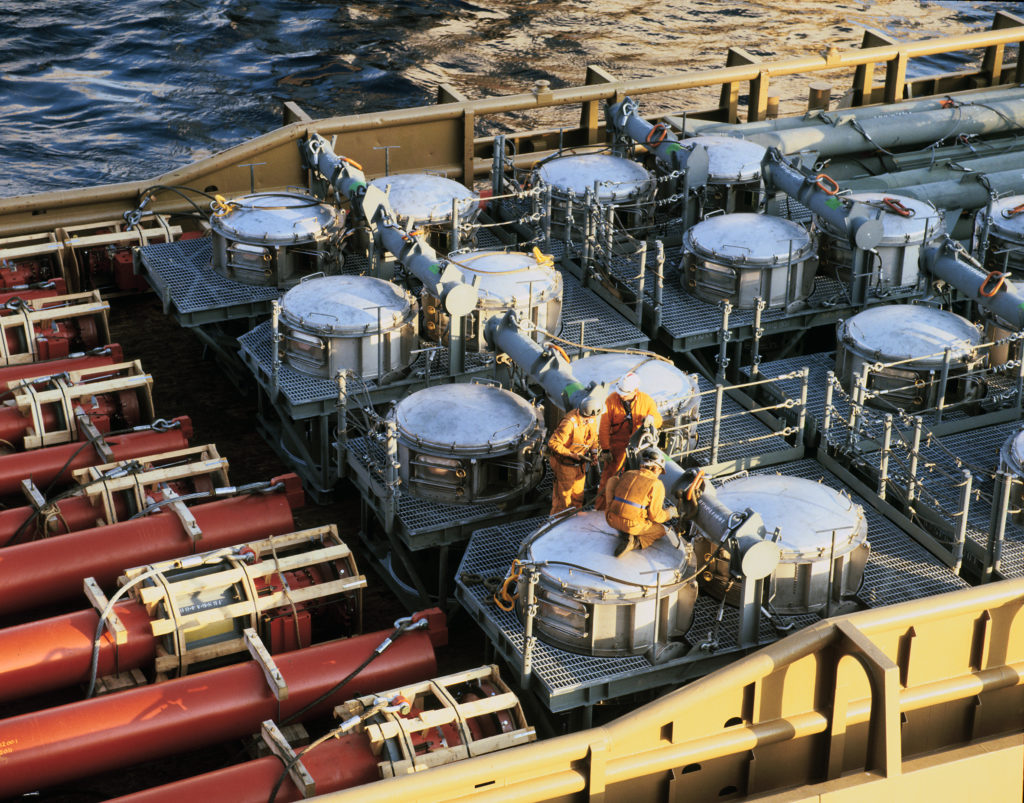
A year earlier, the southern flare stack and the two supports for the connecting bridge had been elevated by more than seven metres using the DB 102 crane barge.
Preparations for the jacking programme began on the platforms as early as January 1987. The first step was to construct scaffolding at every location where work would take place.
A total of 2 500 metres of guide rails with manual cranes were installed, and a number of pipelines and tanks had to be moved to accommodate these.
In addition, 214 hydraulic power units were put in position to supply the jacks. The latter were finally installed and activated so that they took over the weight normally borne by the platform legs.
The first milestone came on 31 May, when the initial cut was made. A metre of leg on the riser platform was removed to provide space for bolted flanges – an ingenious solution which was central to the project.
Once these flanges had been installed, everything was ready for the actual jacking. This began with the hotel, and the jacks were activated at 03.48 on 16 June 1987.
Within just 12 hours, the 10 500-tonne topsides had been raised by 6.4 metres. The extension sections were inserted, and everything lowered into the new position.
The riser platform followed on 15 August, when it was raised six metres in the space of less than a day. And the four platforms south of the tank – P, C, FTP and Q – were lifted on 17 August.
Jacking this quartet and associated pipeline supports simultaneously minimised the number of pipes and cables which had to be cut. Only those running into the tank had to be dealt with.
In the meantime, the northern flare stack and 2/4 G had been raised with the aid of a crane vessel. Since it was the newest platform, 2/4 S was taller than the others and needed no action.
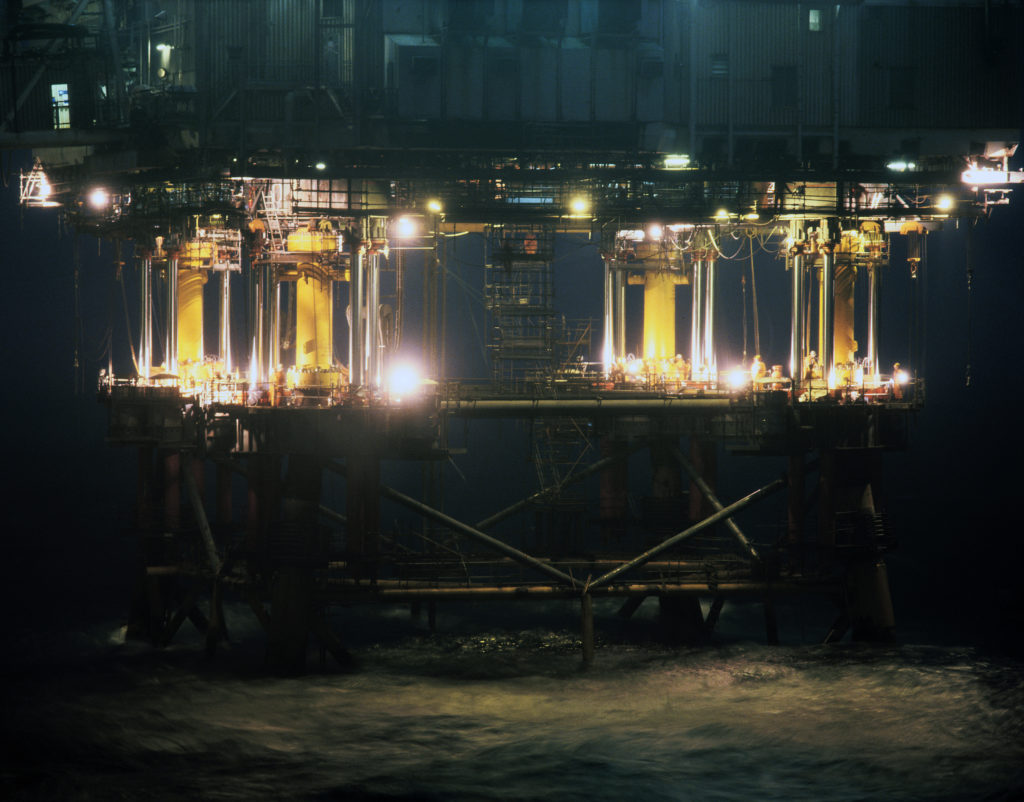
The jacking operation as such had been completed by 18 August 1987. It had taken 14 hours and 24 minutes in all, and involved 2 500 work-days of 12 hours each.
This was followed by removal of the jacking equipment and the work needed to bring the installations back on stream. Ekofisk was in production again on 4 September 1987.
The actual tank could not be jacked up, and it was therefore provided in the summer of 1989 with an additional external breakwater.
Jacking up the Ekofisk structures proved a success, but the seabed subsidence continued – although at a slower pace than before.
Jacking up Ekofisk 2/4 H – step by step
Phase one: preparations
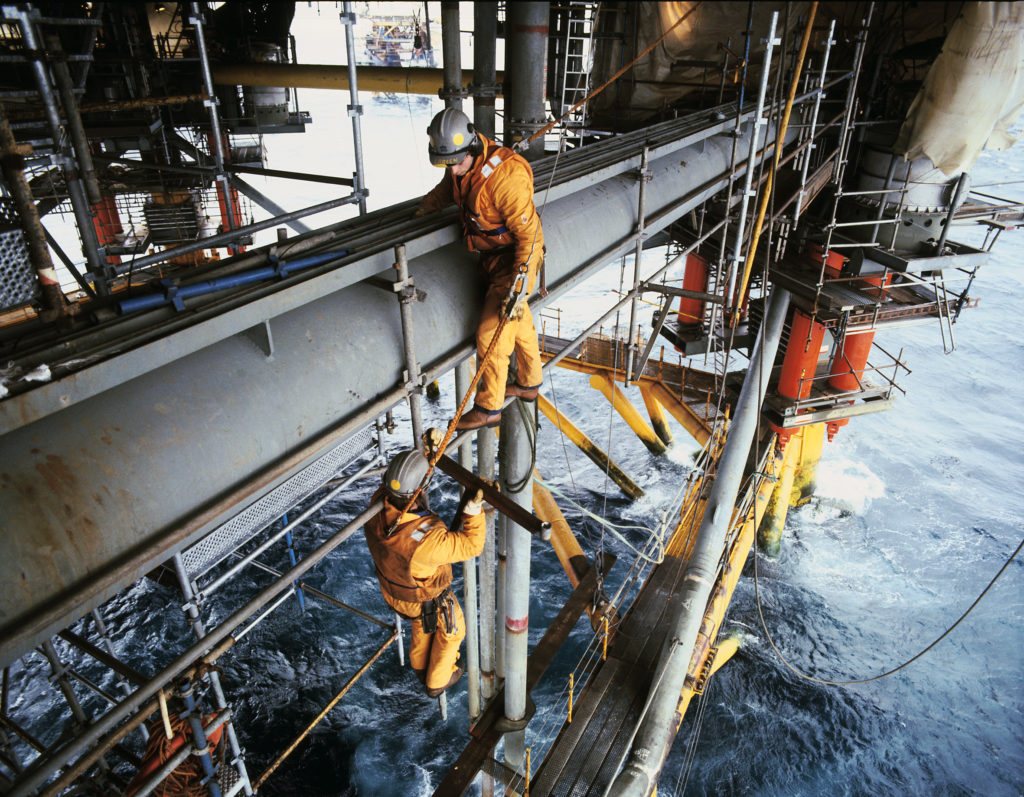
The first step was to install scaffolding, guide rails, support beams, hydraulic power units and the jacks. Four of the latter were installed on the hotel platform’s legs, and two per leg on the other structures. Each platform leg was then cut and fitted with bolted flanges after the topsides weight had been transferred to the jacks. A one-metre section was cut from each leg, with the flanges then inserted and welded into place.
Finally, the gas and oil pipelines to Emden and Teesside respectively were cut.
Phase two: jacking up
A last check of the equipment was conducted before all the jacks were raised to the upper jacking beam and set to a zero reference point.
The topsides were lifted up and clear of the guide blocks. This called for accurate control, and was done in short stages which were carefully checked for each leg by people below.
Once the topsides were clear of the blocks, they were jacked up 6.4 metres with stops along the way to deactivate the flat jacks. These had been activated initially to allow the topsides to move a little in the first phase.
A low-friction teflon coating made this possible without the jacks losing position. Once the flat jacks were withdrawn, the steel-to-steel interface between jack and leg created a rigid connection.
The extension pieces were put in place and the lower set of bolts fastened before the topsides were lowered onto the sections.
While the jacks continue to carry the weight, the upper bolt sets were tightened. Finally, the weight was transferred to the extended platform.
“Can do” attitude
Lars A Takla was manager for partner collaboration and long-term planning, investment budgets and such subjects when news of the seabed subsidence was received in December 1984:
We sent out a ship to measure the water depth, and found that this had increased by three metres. That was obviously a huge shock. A discussion had been under way from the start on whether the reservoir chalk, which as very porous, could collapse. But everyone expected three kilometres of overlying rock to hold. However, this proved so unconsolidated that it subsided.
We began to wonder whether this was the end. A few more metres and we’d have reached the critical wave height in the design criteria for the platforms. Everyone had suffered a rude awakening, and we launched masses of studies to determine what had happened and how it could be countered. The pressure changes which occurred in the reservoir meant production had to be adjusted. But a ‘can do’ attitude prevails in Phillips.
The first reaction was astonishment: ‘Gosh, what can we do about this. It’s an impossible problem’. Then people switched to: ‘We’re going to overcome this’.
At least 30 different methods were discussed. A load of engineering companies throughout Europe were involved, and we received masses of letters with good ideas about how to deal with this. The jacking-up proposal came up fairly early on, but was rejected as a ‘Donald Duck’ solution. It would be impossible with these huge platforms and the masses of piping and cables tying them together.
After going through all the options, however, only jacking-up the steel structures remained. So the platforms were jacked up in 1987 and a breakwater installed around the tank in 1989.
The subsidence meant we had very little time, and had to find a solution quickly. It was a massive job. We produced about 120 jacks, plus the hydraulic actuators and other control systems. The amount of jacking had to be exactly equal to avoid any tilting. Extending cables while the jacks were in action, so that production could continue without interruption, was a huge job.
We had a special team working on all the connections between the platforms. A lot of things were done with the power off, of course. So all these preparations to avoid shutting down were extensive.
Hundreds of welders were at work to attach the jack supports. I came out as offshore manager in the autumn of 1985 and sat in the midst of this work, which lasted until 1987. I was there when the first platform, the hotel, was jacked up. That was almost a trial operation. This structure could not be raised at the same time as the others because a bridge about 100 metres long ran to the tank.
When we started, we had a control room where the jacking director sat. I normally had an office and an emergency response room in the hotel, but we established a temporary centre on the tank.
High winds and waves created about a day and half of delays. We had our own weather forecasters working permanently on Ekofisk at that time, who received reports from every European weather station to avoid starting anything when bad weather was expected.
The hotel is roughly as big as a 10-storey house, and I remember the jacking director saying: ‘I assume you’ve calculated the platform’s centre of gravity properly now, so it doesn’t blow over.’ We could reassure him, because much of the heavy equipment was low down. In any event, it went very well.
Being involved in this was great fun, and I believe it’s one of the biggest-ever engineering achievements here in Norway. I remember we had 3 200 people on the field, and you can then triple that to count everyone involved.
Jacks and spacers were manufactured all over Europe. Everything had to be shipped out, and the timetable was tight. Supply ships came from every port in Europe, representing a huge logistical challenge. But it was fun to be part of this, after all.
At that time, we’d bought a flat in Spain. So I went down there after the jacking operation for a 14-day break. During that fortnight, they jacked the rest of the platforms, so that we were more or less finished when I returned.[REMOVE]Fotnote: Lars A Takla interviewed by Kristin Øye Gjerde, 19 December 2002.
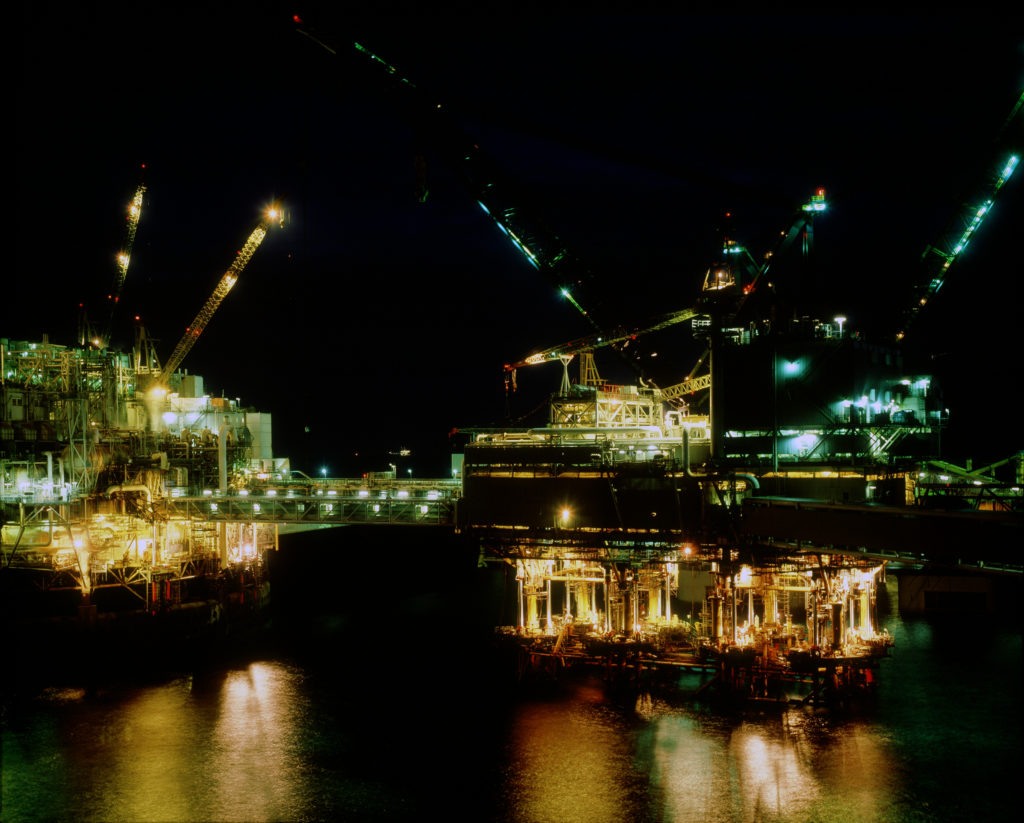
A guide to Ekofisk jacking (info-sheet ca 1987). This is how we elevate Ekofisk (brochure ca 1987). Suppliers to the jack-up project (brochure ca 1987)
Booster platform becomes unmannedSeawater injected into the Ekofisk reservoir