Statoil brings Tommeliten on stream
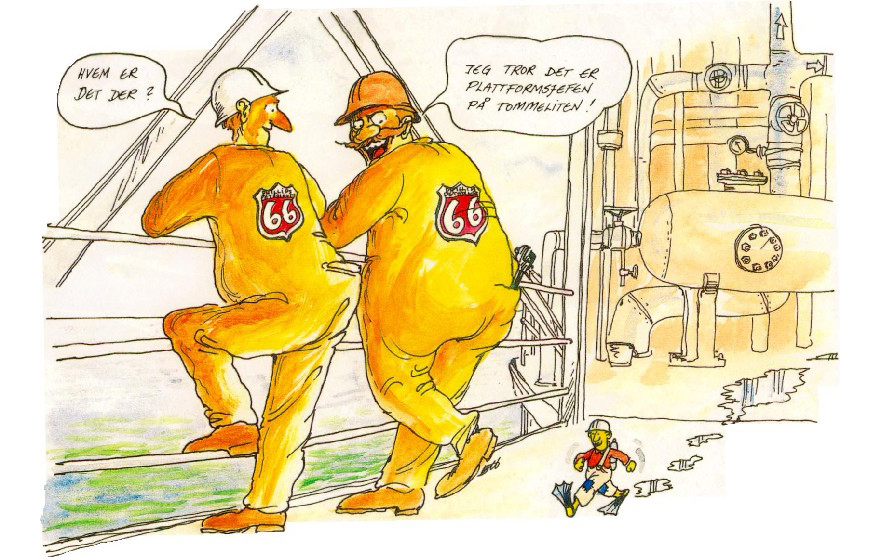
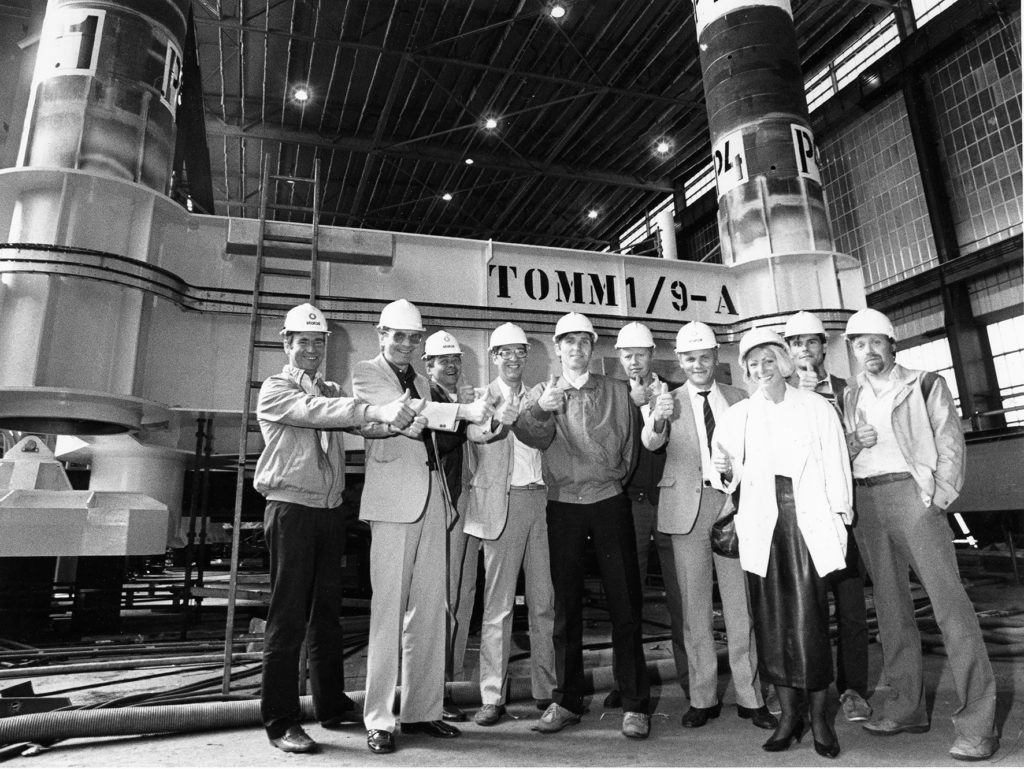
The seabed template, with slots for six wells, was built by Moss Rosenberg Verft. It weighed 800 tonnes and measured 42 x 26 x 12 metres.
Production licence 044 covering Tommeliten was awarded in 1976. The field lies 11.8 kilometres west of Edda and comprises two deposits – Gamma and Alpha.
The original plan called for Tommeliten to be developed with a stand-alone platform supplying gas to Emden. However, this became too expensive after the 1986 oil crisis. Statoil opted instead for a subsea solution. Phillips objected and pulled out, leaving the state company with 70.64 per cent, Fina 20.23 per cent and Norsk Agip 9.13 per cent. Phillips nevertheless had good use for the Tommeliten gas. A little was used for injection in old wells on Edda, boosting its output substantially. The gas injected was later recovered a second time from Edda.
Since the water depth on Tommeliten is about 80 metres, divers did the subsea work. A template was placed on Gamma to speed up the development. The protective structure and manifold were manufactured at the Rosenberg yard in Stavanger while drilling was under way.
Shoelace creates problems

Three subsea monitoring systems were available during the installation of Tommeliten, but both the remotely operated vehicles (ROVs) were out of operation during commissioning.
The decision was taken to send Per Moi down in a Mantis manned submersible. As soon as he reached the seabed, however, the control room heard him yelling “get me up, get me up”.
This sounded strange to the American supervisor, because the vehicle had only just reached bottom. But Moi had got his shoelace stuck in the Mantis hatch, which was enough to allow water intrusion.
Loose screws and bending pipes
A number of other accidents occurred. The screws used to attach the handles to the valves on the operation panel for each well eroded. Normal unbrako screws had been used, but their sockets had vanished. Divers were used to replace them all with the right metal and external slots.
When the template was inspected before production began, a number of bolts turned out to be missing from the flange holes and were lying on the seabed. Two diving support ships, including Seaway Pelican, spent four weeks replacing all the bolts in the pipe flanges on the template, on the pipeline and beneath Edda. That delayed start-up.
Statoil laid three underwater pipelines to tie Tommeliten back to the Edda platform – two production lines and one for testing. Output from the field then entered the Ekofisk system for onward transport to Emden.[REMOVE]Fotnote: PhillipsNytt, October 1988 and no 3, 1987.
After allowing them to warm up, the pipelines were inspected. Specialists had conducted a long discussion over whether the trenched pipes should be covered with gravel or left for nature to do that job. The heated pipelines were meant to curve between the trench sides rather than escape from it. Those who favoured covering were dubious about this, since friction would differ from place to place.
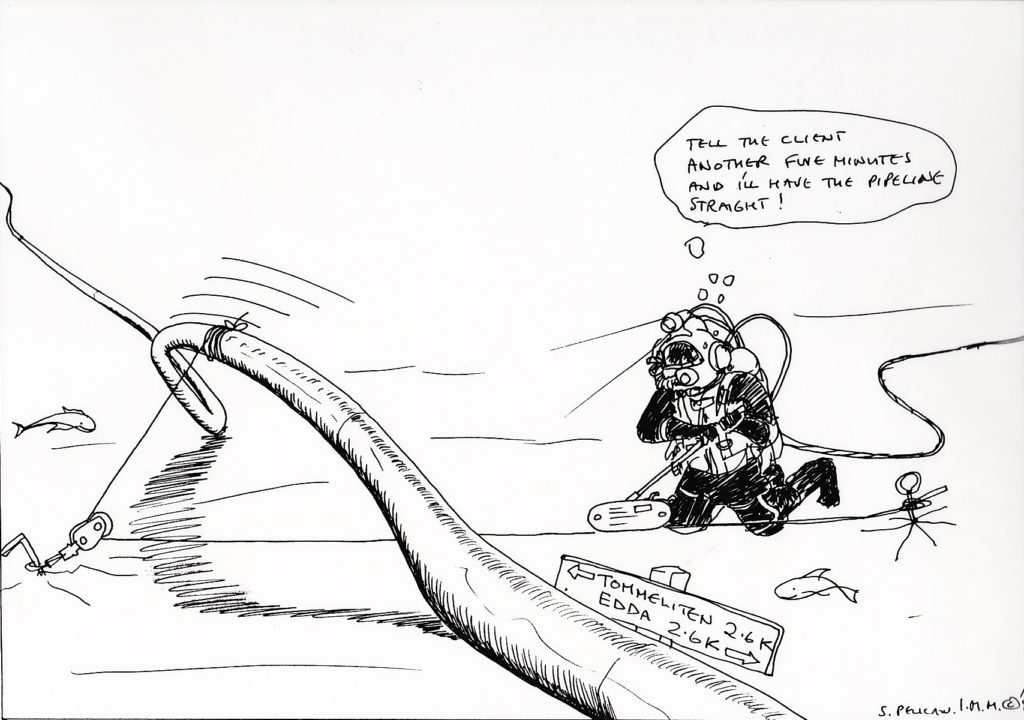
Inspection showed that the pipelines had escaped from the trench in several places. The worst case of this “upheaval buckling” was about 30 metres long and 5.5 metres high. It looked as if the pipelines had come to life. Measures were needed to stabilise them.
The decision was taken to attach cement supports cast in situ. Specially manufactured plastic “tents” with attached straps were made fast to the pipelines by divers and reached down to the seabed. Each chute had several pockets which were filled with cement through a hose from a ship, starting at the bottom and moving gradually up as each pocket made contact with the pipe.
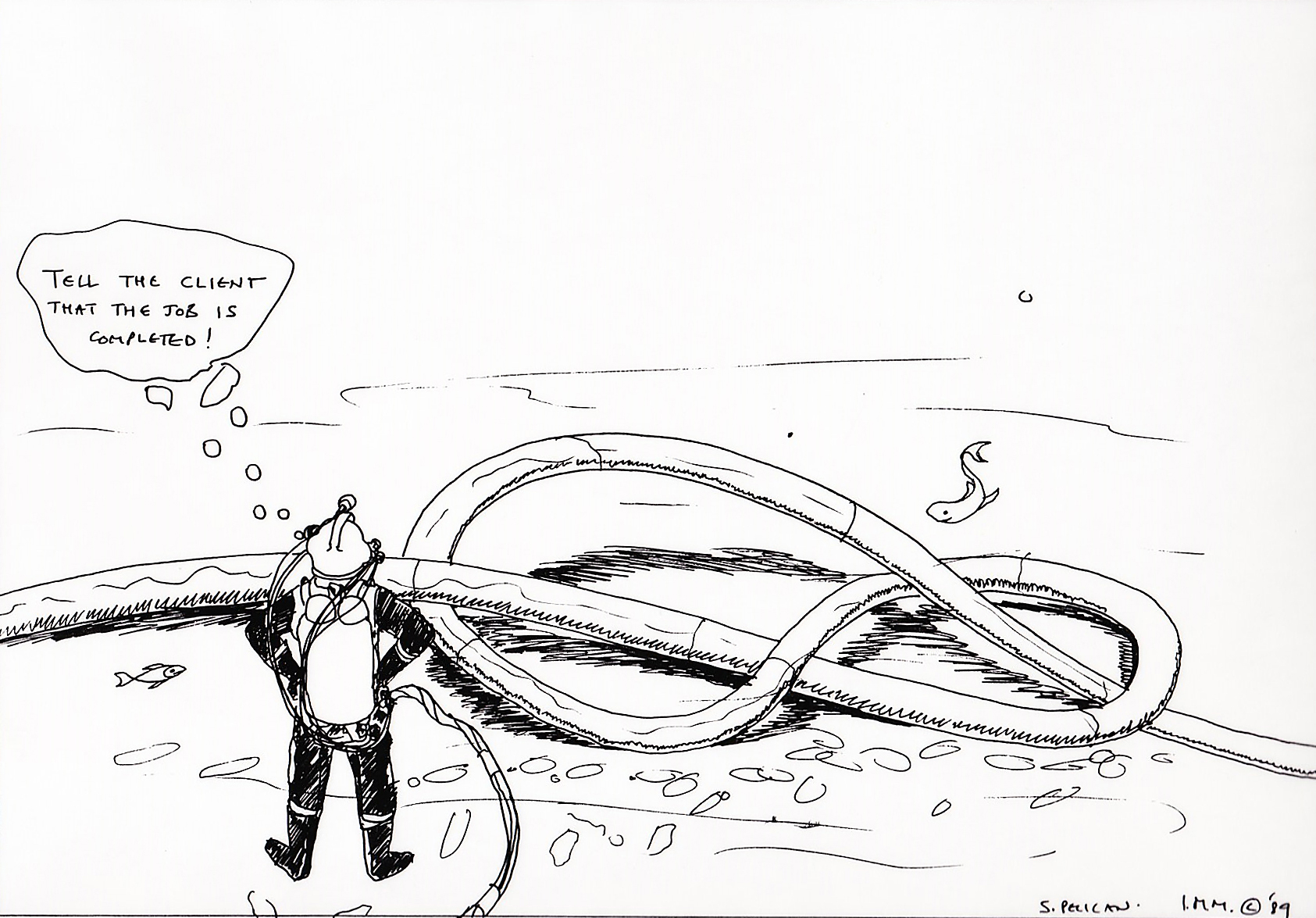
Gravel was subsequently dumped at six upheaval points in an optimum manner which dispersed it both under and over the pipelines. Dumping alone was used for the smallest cases. It took a boatload totalling 8 000 cubic metres of gravel to ensure that the transport lines were securely pinned down and could be overtrawled.[REMOVE]Fotnote: Hans Birger Hansen interviewed by Kristin Øye Gjerde, 1 December 2015.


