Operations and well workovers
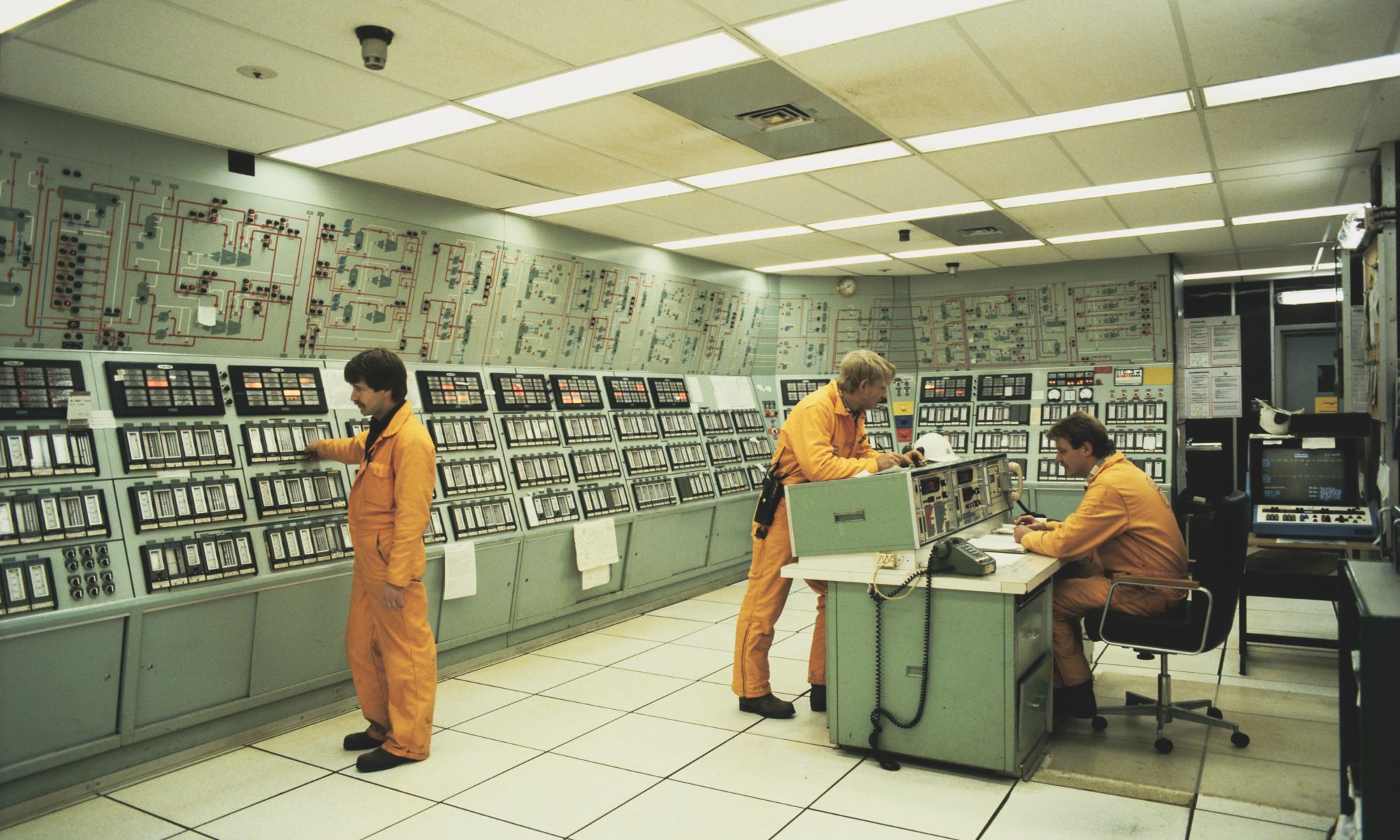
To ensure that the wells produced optimally over time, they needed workovers and stimulation. That was the province of people employed by various service companies who handled such work.
Operations supervisor
Previously known as the production supervisor, this person is in charge of the process operators. They will usually have an engineering background or been promoted from an operator job, and will be particularly well trained in safety work.
Process technician (operator)
A process technician has an overview of everything related to electricity, water and diesel oil supplies, and naturally of the whole process from the point when oil and gas arrive until they are exported by pipeline.
These technicians monitor, manoeuvre and manage this flow with the aid of computerised systems in the control room, checking that the process is progressing as it should.
Another important part of their job is checking on the equipment out in the process modules by conducting physical inspections.
The actual production process takes place in closed systems which cannot be directly observed, so that continuous monitoring of the computer screens is important.
Process technicians regularly tour the modules to check pressure and temperature. Before the computer age, they read off such data directly from metering instruments. Other duties may include establishing the dew point of the gas and taking oil and water samples.
All results are carefully logged. Being thorough and accurate are important characteristics for somebody working with the process.
They must ensure than any abnormalities registered are corrected. If this is beyond their abilities, an electrician or mechanic must be called out. Since production continues around the clock, the process is based on shift working.
In the Ekofisk Complex, process technicians may have to reroute process streams when certain sections of the plant are shut down for maintenance. They do this under the direction of an operations supervisor or a superintendent.
Before the conversion to Ekofisk II, process technicians tracked all important production data from the Greater Ekofisk Area fields via computer screens in the control room on 2/4 T.
Every other minute, their computers harvested information from the other installations. Should a crisis occur, an outlying platform could be shut down by one push on a button.
These operators also monitored oil and gas transport through the pipelines to Teesside and Emden. If the quantity of crude sent to the former was greater than the amount which arrived, they were alerted to a possible leak.
From 1998, the control centre was transferred to the new Ekofisk 2/4 J platform.
Roustabouts
Roustabouts are used in various activities, such as assisting with drilling, helping production or maintenance work. They may also serve as heliguards.
Along with the crane operators, they are responsible for most transport of goods and equipment to and from the drill floor and also do a range of preparations in that connection.
Earlier, roustabouts also handled external cleaning work on the platform – rust chipping, scraping, painting, washing of bulkheads and decks, water jetting, and lubricating crane parts, jacks, lifeboat systems and so forth.
They also did much of the manual mixing of drilling mud and assisted the derrickman in cleaning rooms, tanks and equipment used for such mixing.
Crane operators
These do an important job on the field by ensuring that necessary equipment is lifted from the supply ships and that waste goes the other way.
Cranes in the Greater Ekofisk Area (GEA) handle some 100 000 tonnes of goods per annum. Earlier, personnel were also lifted up from or lowered to supply ships on baskets.
In 1991, there were 130 crane operators in the GEA, including 40 at the Ekofisk Complex.
Important qualifications for this job include patience, mental calm, and good eyesight and health. Safety is the first commandment.
People must keep an eye out for suspended loads at all times, and the crane operator always has overall responsibility for safety on deck.
Good collaboration between crane operator, banksman and helmsman is crucial when lowering cargo to the deck of a supply ship. They stay in contact through headsets and microphones.
The helmsman keeps the ship in a fixed position, while the banksman’s job includes ensuring that the load has been correctly suspended in good-quality slings.
For safety reasons, the equipment must be in tip-top shape. Every crane is overhauled every 14th day in addition to daily inspection by the operator.
The cranes contain a small computer which monitors the load on their booms. From a screen, the operator can read off boom angle, maximum load in that position and the load on the hook. Visual and aural signals alert them if the permitted load is exceeded.
Data on all loads are registered and sent to land for further computer processing to build an archive of the stresses imposed on each crane. That improves the ability to check and predict its condition and to avoid fatigue fractures, for example.
Well service operator
Failure by a well to produce as expected is usually a sign that the reservoir pores close to the perforated zone in the well have become clogged. A workover is then required.
Various chemicals are used to clean out the blockages. In the Greater Ekofisk Area, wells have traditionally been stimulated using a hydrochloric acid blend.
The acid is brought out by supply ship and pumped down the production well and into the reservoir at a high rate. That usually works well.
However, well service operators have many other duties and are generally specialised in certain areas. That includes work with drilling, testing and maintaining producing oil wells.
Key tasks involve installing, manoeuvring and repairing equipment and machinery, and executing and monitoring these operations.
On the basis of their own observations, analyses, measurements and instrument readings, these personnel must be able to assess and take independent decisions on managing well service work.
Many of these operations are conducted in wells under pressure, and the threat of losing control – resulting in a blowout – demands vigilance and precision.
Well service operators use electrical, pneumatic, hydraulic and motorised tools, machinery and equipment for various jobs. They must be familiar with wirelining, hydraulic tubing, completion, cementing and drilling.
This job title incorporates such earlier occupational categories as casing operator, cementer, wireline workers and snubbing personnel.
Wireline operator
This discipline covers running a steel cable (wireline) into a well to conduct mechanical or electrical operations, and is used for both drilling and testing production/injection wells.
A qualified wireline operator will manoeuvre and install advanced equipment down the well to secure data on the formation, the reservoir, production properties and changes over time.
Well maintenance utilises either a drill string made up of jointed steel tubes, or a wireline about five-six millimetres in diameter wound on a drum.
The latter can be used to lower various tools into the well or inside the string in order to carry out different jobs. Valves can also be replaced or wells logged.
Moreover, “fishing” tools can be attached to the wireline in order to retrieve objects which have been lost down the well.
Coiled tubing is a relatively new technology developed in the 1990s, which has proved ideal for well maintenance to ensure optimal production.
This solution involves a continuous length of tubing which can carry equipment downhole. With a smaller diameter than a normal drill string, it is coiled on a large reel and straightened out before entering the well.
A wireline operator works on both fixed and mobile installations where exploration and production drilling and oil/gas production are pursued. They will also be able to work on land in preparing, maintaining and repairing wireline equipment.